Power management solutions
Project brief
The site we visited employed staff whose role it was to specifically look for potential risks to quality. Because of this, the pack had to go through many sign-off processes to get approval. A highly complex manufactured part used in aerospace products, the stator is a highly delicate part requiring an extreme degree of care when handling. If a consignment was dropped or knocked it remained largely unchanged to the human eye. For this reason, the new pack had to go through a rigorous sign-off review and withstand a lot of scrutinies.

Design and Development
The engineers had limited space on the assembly lines. Initially, the design had a lid incorporated into the pack; making it more cost-effective. However, this single-piece design took up too much space on the assembly desks. For this reason, a lid that could be placed under the main box was the perfect solution. The lid was also a very good place for paperwork that went with the consignment during its manufacture. Two sets of divisions were designed to protect all product sizes within the range of 15 products with different diameters and heights giving a universal pack with minimal origination and manufacturing costs. The divisions had to have a smooth, non-abrasive top edge to ensure the wires of the stator product did not get damaged when and if rubbed against them during use. The lid protects the part from the environment when stored. The pad design is a crucial part of the overall pack for this customer. Protecting the product from shock when it is picked up and placed on hard surfaces, the pad uses the properties of hard plastic correx extremely well. Creases in the folds of the extended flaps act as an upward going force. In this way, the floor of the pack absorbs any shock when the stators are placed into the box and when the box is placed on shelves or desks. Ergonomics played a vital role in positioning the handholes so that 4 fingers can be placed into the grey hand hole and a thumb could be placed onto the top of the pack giving maximum grip/hold. It was noted that this part of the design was a sea-change for the engineers. Also, crucially the hand hole did not take up much room. A valuable commodity at the site!
The new design incorporates many attributes to create a sturdy, easy to use pack that fulfils all required purposes to reduce potential damages and risk. It is made from 400gsm 2.6mm correx material. The project cost in comparison to historic damages agreed with site managers was £14,000, giving a nett saving of £9,800 annually. Notwithstanding the time wasted to inspect parts that might have incurred damage. The new pack needed to be completely protective of these high value, highly fragile parts.
Images
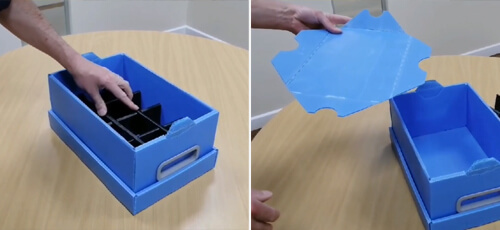