Design, manufacturer and distributor
Project brief
We were contacted by our client. to look at re-designing an existing pack as it was proving too labor-intensive to assemble and not providing enough structural support during transit. The existing legacy packaging box was a long modified 0471 which was hard to assemble via x1 person due to how a FEFCO 0471 tucks in at each end, thus taking on average up to x2 persons a total of 85 seconds (equates to x1 @ 170 seconds) to package the product. As the customer was manufacturing and packing over 22,000 units/ annum – This was amounting to a huge cost in labor, approximately 1038 hours per annum.

Design and Development
Over the course of seven months, we worked with the customer producing multiple samples with the sole aim to reduce assembly time as much as possible and improve protection/retention of the product wherever possible.
The carton also makes use of another neat solution in the form of tapered postal locks to help improve durability during the supply chain, the tapered locks prevent the tabs from accidentally opening and thus adds a security element. The design fundamentally works by folding each end integrated fitting to retain the product in all axis’ and then by having a larger “cross-brace” section of corrugated which finally folds in between the fittings and prevents them from ”fan-folding” out during transit. This “cross-brace” also has a second function whereby it houses the accessories which are the first thing the consumer sees upon opening. This helps ensure the accessories are accounted for upon opening and not forgotten, as can happen in other packages.
The pack is a 1-piece die-cut to help streamline the manufacturing process and ensure recyclable credentials at its end of life.
The artwork is functional with good impact and consists of branding, consumer information, and a technical drawing of the product detailing how to purchase spares, etc. As the box will not be point-of-sale, our client has developed the artwork as to give the consumer as much information as possible regarding the product whilst retaining a professional finish.
The final design was not only faster to assemble (x1 person @ 50 seconds which equates to a labor reduction of 70%), more durable and much more aesthetically pleasing, but was more cost-effective from a material cost point of view. The final design has also passed an in-house drop test whereby the product was unscathed after being repeatedly dropped onto all faces from a set height.
The approved design was able to perform on the points above due to the application of carefully engineered integrated folded fittings that are triangulated to increase stability and protection.
Images
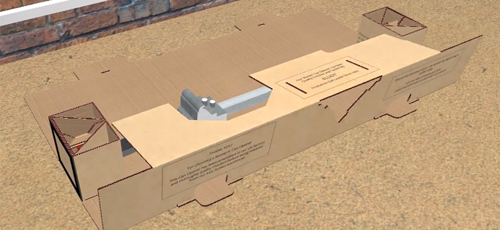