Packaging for the electronics industry
Packaging for the electronics industry
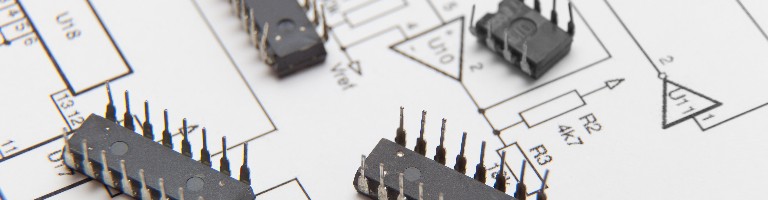
At Kite we understand that electronic packaging requires a greater amount of protection, and need to adapt to a large scale of various product specs. That’s why we have developed specialist solutions for big or small electronics products, to protect them from common damages this industry faces such as mishandling and static or conductive charges whilst in transit or storage. We have recognised that the need for high quality products in this industry is of the highest importance, which is why our team has developed its technical knowledge, skills and testing expertise to ensure the development of the best quality products to this industry.
We can also offer the required bespoke service package for the electronics industry from our extensive offering.
These include:
- Kan-Ban – Kite will organise monitoring and replenishment of packaging products when they reach re-order level
- Stock and supply – Kite is able to store product in its own premises and provide product on a call off basis
- Just-in-time – When a customer’s production schedule requires packaging at specific times, Kite can hold stock in their own premises and deliver at an exact time slot straight to a specific point in the line
- Quality inspection – Kite will ensure each and every product is tested and fully audited so that it is of the highest quality and will provide all the relevant quality specific documentation
- Technical drawings – Packaging technologists to develop products that meet exact technical requirements.
- Full drop-testing service
For further details of these offerings go to Service.
Product offering
Kite offers a number of packaging solutions for electronic products for manufacturers, distributors and retailers specialising in this area.
These include:
- ESD Packaging
- Shielding bags
- Conductive bags
- Suspension / retention packs
- Jeddec trays
- POS packs
- Anti-static foam-lined cartons
- Blended films
- Thermoforming
- High quality print process for various substrates
- Printed tapes
- Labelling – REID (Radio frequency identification)
Electronics case study
Project brief
Kite was approached by a world-wide manufacturer of electronic products, with sales in 100 countries, and a well-known brand for computer printers. The problem they faced was initially with the packaging of their ink cartridges, for which they used a FBB - folding box board solution (typically used for cosmetic and some food packaging).
This was the traditional method of packaging, however in the early 2000’s retailers identified that small high value electronic items were easily pilfered from the paper packaging, and started to introduce secondary packaging, whereby the packaged product was packaged within a secure clear plastic casing – which was initially applied and removed by the retailer. However in time the requirement to apply the additional secure packaging was driven back to the original equipment manufacturers and suppliers to provide.
This customer initially used blister clamshell packs that were securely ultrasonically welded together to form packaging which is often impregnable. This packaging method can be relatively slow and created production bottlenecks in high volume manufacturing.
Kite was therefore tasked with a better packaging solution which would both benefit the supplier, their customers and would improve the packaging process in the warehouse.
Design and development
Kite first introduced a form, fill and seal machine concept, as used in the food industry, to streamline the packing process. This system involved taking a reel of rigid extruded plastic and formed a base moulding, parts were packed directly into the forming (no carton box) and a header card / paper was used to identify the product and to give a point-of-sale. The pack was then sealed using a clear top lidding film.
Further innovation involved Kite working with its printing suppliers to take the technology of printing on rigid plastic films, such as credit cards, into mass production for this customer to replace the printed paper header cards. Ink cartridge suppliers by their nature require a good quality print to portray their product and the technology provided with our print process allowed them to push the boundaries of the printed packaging content. Bold, vibrant images were used and printed direct onto the rigid films providing excellent point of sale products.
This also solved another key issue of the customer which was the prevalence in the ink cartridge industry of ‘grey imports’ and counterfeit products. Copies were so accurate that they could not be easily identified in the retail environment, but by adapting this new method of packaging and printing which were harder to replicate, a new security method to prevent counterfeiting was automatically adopted.
Testing
The customer already had strict drop and vibration transit test requirements for all of their packaging. With the new system Kite put in place a new requirement to test the burst strength on the weld seal opening was also incorporated, developed by the Kite team using previous expertise.
The new product passed all tests and has been incorporated as the only packaging for ink cartridges by the customer.
Result
This customer has been a long-term client of Kite’s and we continue to create on-going material and printing developments to continually improve the high quality at the best pack cost.